How To Use 2-Part Silicone for Crafts. Silicone Kits
How to use 2-part silicone for crafts? People think that all 2-part silicones are the same, but they are not. In my career, I have used many different silicone rubbers, and they vary from manufacturer to manufacturer.
It is important to find one where air entrapment is less likely to occur. This quality is especially important for the smaller and more detailed your model may be, and the material that will be chosen to produce the final product.
Knowing Ahead of Time
Unless you are aware of the issue of air pockets (entrapment) You may not think it is to important point, but after you’ve made a few molds and cast some pieces, you will realise just how critical it is. So knowing at the outset helps you to choose right.
We promote transparency. This post or site may contain affiliate links. This means that only if you make a purchase through these links, not just by clicking, I/we may earn a small commission at no extra cost to you.
As an Amazon Associate, I earn from qualifying purchases
2-Part Silicone & Air Pockets = Pits.
Any little air pit in your mold will show as a little bump on your finished piece, which is not that important on a huge piece of cast stone as it will be hard to notice. But say it’s a copy of a beautifully small carved piece; it will show, and it will take some skill to remove it and make it disappear.
Candles and soaps are a lot easier to deal with as they are soft and forgiving products to tweak.
So, remember, when you pour your silicone mold, it will only reflect the finish and detail you have put into your model piece.
If your model has a nice, shiny, smooth surface, so will your silicone mold and any future castings.
2-Part Silicone for Crafts, Your Crafts.
After you have decided what your craft pursuits are going to be, another major consideration is the heat ranges that the 2-part silicone of your choice or other products used for molds can withstand through the whole manufacturing process.
Each craft does vary, and if you are thinking of making items from different casting materials, you need to know the maximum heat levels generated in each manufacturing process.
For Baking.
This is quite easy for some items like baked goods, or freezing/chilling of some products. But what about your resins, waxes, soaps, or polyurethane products, They do vary considerably. Its best to use silicone at a higher temperature.
Some products create their own heat in the process (exothermic heat) when mixing in the hardener or resin, for instance. And if you make a slight mistake with the hardener, meaning too much, boy, oh boy, does the heat go up.
“Cooking it is one term that has been heard for this. Not only is heat generated, but the product changes color and on larger pieces, they warp. Below is a list of some products and the temperature ranges required. More details will be shared when later articles are published about these different products.
Just choose one with a higher range than you expect to give a little room for error.
Check out the claims that each manufacturer makes of all of the products properties, and where possible, ask for samples and, most certainly their detailed instructions for it’s use.
Temperature Ranges Required for 2-Part Silicone Molds.
A, 2-Part resins 150 – 170F (65 – 77C)
B, Candle Wax
Paraffin Wax Comfort Blend melts or mixes at 180–5F (82–5C) and pours at 160–71F (71C)
Soy/Paraffin Blend: melt/mix at 185–200°F (85–93°C) and pour at 160°F (71°C)
Other paraffin Waxes melt/mix at 180–5F (82–5C) and pour at 150–160F (65–71C)
C, Soap. 120-130F (49-54C)

D, Casting Polyurethane 140-160F (60-71C)
E, Concrete. I don’t know the exact temperature at which this occurs, but I have seen poured concrete melt the polystyrene molds when an accelerator has been used over zealously. But it has to be over 400 °F.
And the 2-part silicone that we are reviewing today is good for 400F+, so it covers all of the above uses.
Sizes Available.
For more information, click here 32-ounce Kits (2 x 16 oz)
For more information, click here 64-ounce Kits (2 x 32 oz)
For more information, click here 1 Gallon Kits (2 x 56 oz)
For more information, click here 2 Gallon Kits, 2 x 128 oz
For more information, click here 10 Gallon Kits (2 x 5 gallons)
Coloring 2-Part Silicone.
The coloring of silicones can be very important in some industries that use them, especially if it is a silicane product they produce, like cookware.

In the crafting world or other production companies that use this 2-part silicone product for their molds, colors can be used to color code the group to which the mold belongs. Which is very useful when you build up a stock of molds, whether they are small or large.
Another use is to year-date the year the mold was made, helping to track wear and tear and usage.
There are various forms of colorants available, and nearly all are suitable for this grade of silicone. Liquid pigments, silicone-base pastes and gels, powered pigments, and mica powders—the latter are more suitable for the finished product as they add a sparkle to your silicones.
There are inks and dyes, but many don’t work, and unless you have researched them in detail, stay away from them.
Release Agents.
When it comes to release agents, they are not needed for the production of most products. Allowing an occasional spray with a silicone product helps with maintenance and longevity. It behaves like a conditioner.

Some production products do better with a release agent, such as 2-part silicone to 2 part silicone, epoxy resin, polyester, and polyurethane resins. There might be others, but I doubt you will come into contact with them.
Now at the model-making stage, its best to exercise caution. A possible procedure is to spray your model and casting/retaining frame with silicone release and brush them out with a good brush to get into any awkward areas, as if you don’t, the silicone will get in there and be such a pain to demold. And then mixing your silicone, just before you pour another light spray.
2 Part Silicone & Mixing & Curing:
Before use, be sure that Parts A and B are at room temperature and that all tools are ready for use. The surface and air temperatures should be above 60°F (16°C) during application and for the entire curing period.
Always read any product labels or other instructions. Some products say by volume, but it is best to check the weight of the 2 containers that the material comes in, which should be on the label and if they are the same, it is a good practice to go by weight. Note that not all products are 1-1 or 50–50%.
Weighing
Carefully weighing of 2-part silicone is crucial, Part B and then part A in proper ratio into a clean mixing container. Accurate weighing is essential to obtaining the optimum physical properties from the cured rubber.
The best way is to use a clean container for A & B and a larger container for mixing them 2 together. A coat of molding wax applied inside your mixing containers will, in most cases, let you peel off any remains after the material has set. Adding part A to part B is a good habit to get into.
Mix thoroughly, scraping sides and bottom of the container. Making a good job of this will help with the final product, and try not to add to much air into the mix to avoid any air pockets in the molds. If you decide to use a mixing drill, make sure the mixing paddle is suitable, and still use a clean piece of wood to scrape the sides occasionally.

Follow the Instructions
If you follow these instructions and pour your 2-part silicone slowly, similar to the resins, this should ensure an air bubble-free mold without the need to deaerate/degas the product.
Now we can Take a deeper look at Cast-A-Mold Platinum; it is one of the best I have used and cost-effective in its product category. There are many others and I will go in to them in other articles.
Food-grade 2-part silicone rubber for mold-making from specialty resins.
Create the perfect 2-part silicone mold with Cast-a-Mold Platinum food-grade silicone rubber, making it ideal for creating durable molds of any shape or size.
This versatile food-grade platinum (addition ‘Glossary‘)-cured’silicone rubber is designed for a wide variety of mold-making applications.
It’s curing process is known for its assistance in creating high precision and stability, resulting in silicone that has excellent properties such as low shrinkage, high tear strength, and long-term durability.
This 2-part silicone is often preferred for applications requiring high performance and reliability, such as food-grade molds, because it does not produce by-products during curing and has a longer shelf life compared to other types of 2-part silicone
It offers outstanding performance with its 1:1 mix ratio (by weight, not volume); it has a low viscosity, excellent tear strength, tensile strength, elongation, and heat deflection.
Applications for Custom Molds:
Cast-a-Mold’s Platinum Food Grade 2-part Silicone Rubber has uses that go far beyond just crafting custom resin molds. It can be used to make translucent silicone molds for a variety of other projects, such as:
- Casting candies and chocolates
- Casting polyurethanes
- Epoxy resin casting
- Polyester resin casting
- Cement
- Cast Stone
- Soap making
- Candle making (and other wax applications)
- Plaster
- and many more!
- Cast-A-Mold Platinum 2-part silicone is user-friendly and FDA-compliant, ensuring safe use in food-related applications. Its ability to cure at room temperature is another huge advantage; this eliminates the need for specialized equipment or degassing in vacuum chambers.
Tips, Tricks And a Few Notes Cast-A-Mold Platinum Food Grade Silicone Rubber:
If You Require a Super-Fast turn-around on a Mold, platinum-cured silicone rubber can be heat-accelerated. For instance, if you expose the mold to a temperature of 150°F (65°C), the curing time will be significantly reduced from 8 hours to just 30 minutes.
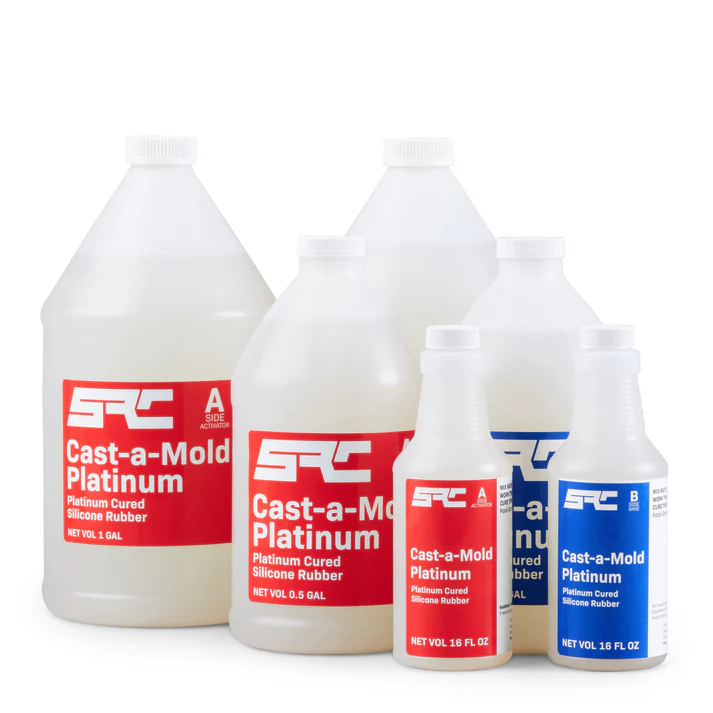
IMPORTANT.
For food applications, it is recommended to wash the cured mold with soap and warm water before using it, rinsing well to ensure cleanliness and hygienic standards.
Addition-cure 2-part silicone rubber may be affected by certain contaminants, which can lead to tackiness on the surface of the mold. To avoid this, it’s best to steer clear of materials like latex, sulfur-based clays, tin-cured silicone rubber, amines, nitriles, and organo-metallic salt-containing compounds.
Test
If you’re uncertain about the compatibility of the substrate being molded, it’s always advisable to conduct a small compatibility test beforehand. Additionally, applying a clear acrylic lacquer or paint on the pattern can help prevent inhibition. However, this does not apply to polyurethane and latex being used or coated in this context.
Available Sizes.
For more information, click here 32-ounce Kits (2 x 16 oz)
For more information, click here 64-ounce Kits (2 x 32 oz)
For more information, click here 1 Gallon Kits (2 x 56 oz)
For more information, click here 2 Gallon Kits, 2 x 128 oz
For more information, click here 10 Gallon Kits (2 x 5 gallons)
Specifications.
Mix Ratio: 1:1 by weight
Working Time: 40.0 minutes
Demold Time: 8.0 hours
Heat Tolerance: 400°F +
Tensile Strength: 580 psi
Elongation 500%
Tear Resistance: 160 ppi
Color Semi-clear
Hardness 20-A
Viscosity: 10,000 to 12,000 cps
This product is comparable to Smooth-on Mold StarTM, Smooth-SilTM, SORTA-ClearTM, EcoflexTM, and Dragon SkinTM silicones
Contact.
We hope you find the information useful, but if you have any questions or need help, send us a message. You do have to sign in and confirm these days to comply with government rules. Sorry for the inconvenience.
Author Rob
Ps. This is the company that taught me how to build this site and 3 others in 6 months, they keep their promises.
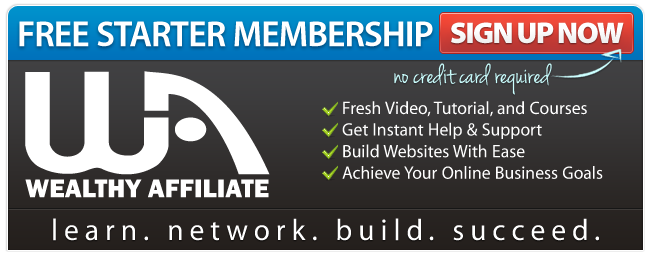